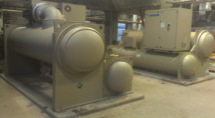
Saint Elizabeth Hospital
Central Utility Plant
St. Elizabeth Hospital, located in Appleton, WI is a comprehensive health care facility offering primary and specialty care services to residents of Northeast Wisconsin. The hospital was founded in in 1899 by the Daughters of the Sacred Hearts of Jesus and Mary, a part of the Franciscan Sisters order. Approximately 375 licensed patient beds and 350 medical staff serve the local community. In 2012, the hospital announced a plan for significant upgrades with capital investment in excess of $100M. The largest part of the renovation included a 5-story patient bed tower on the Northeast side of the hospital campus. As part of the improvements and additional square footage add, the hospital needed to increase the capacity of the central chiller plant. There was also a strong desire to improve chiller plant efficiency and reduce operating costs as part of the chiller plant overhaul. Affiliated Engineers, Inc. located in Madison, WI became involved as the lead mechanical engineer. Tweet Garot and August Winter & Sons, Inc served as the local installing mechanical contractors and Masters Building Solutions provided consulting services and equipment to reach the hospital's goals.
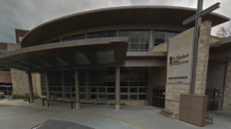
The upgrade to the centrifugal chiller plant included the installation of two Daikin WME700 chillers (above right) with sustained efficiencies that are unmatched in today's market. The chillers utilize oil-less magnetic bearing compressor technology which offers premium full load and part load efficiencies that are sustainable over the life of the chiller. The compressors "levitate" on oil-less bearings and do not require any oil in the refrigerant which provides excellent efficiency with zero friction losses. The design also reduces yearly maintenance costs in terms of oil samples, oil pumps, oil filters, etc. Focus on Energy contributed over $63,000 in rebates to the owner due to the selection of these premium efficiency machines. When the WME700 machines were compared to traditional oil centrifugal machines, the payback was under 5 years for the frictionless compressor technology. After that, the hospital can expect to have 20-25 years of $25,000 to $30,000 savings per year.
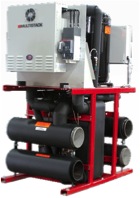
During the design phase, St. Elizabeth Hospital indicated that they have a need for simultaneous heating and cooling for most of the year. This would be very typical of many hospital facilities. There are MRI machines, computer rooms, and other imaging equipment requiring year-round cooling. At the same time, the mechanical system has VAV boxes and reheat coils for humidity control requiring year-round heating. In a traditional system, the chillers would pull heat out of the building chilled water loop and reject that heat out at the cooling tower. Simultaneously, the boilers in the building would burn natural gas to produce heat for the building heating loads. Rather than waste the heat that the hospital already paid to collect at the main chiller plant, the design team decided to implement Multistack Dedicated Heat Recovery (DHRC) chillers. These DHRC chillers (right) provide approximately 100 tons of cooling to the chilled water loop. The heat the chillers pull out of that loop is transferred or recovered to provide 150⁰ water on the condenser side of the DHRC machine. That 150⁰ water, instead of wasting its heat at a cooling tower, is sent into the building heating loop for 1,700,000 btus of free heat. Every btu of heat that the DHRC chiller recovers is a btu of heat that the boiler does not have to produce by burning natural gas. Typical paybacks are less than a year for applications with large simultaneous heating and cooling loads.
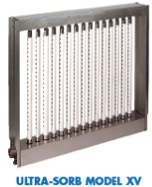
The final piece of the mechanical puzzle involved humidification for the new bed tower and hybrid surgery areas. Six DriSteem Ultrasorb model XV, humidifier grids (left) were installed in the mechanical spaces. Together they are capable of producing approximately 1,500 lbs per hour of humidification for the hospital and are fed from a boiler loop at the facility. The XV humidifiers do not require steam jacketing and include high efficiency insulated tubes that reduce unwanted airstream heat gain by approximately 85% compared to conventional humidifiers. The insulation also significantly reduces condensate production so that the steam the boilers produce goes where it is intended in the building vs down the drain. The humidifier contains an integral condensate management system which is an industry first for pressurized steam. The XV design includes a secondary heat exchanger to vaporize any dispersion-generated condensate and also returns pressurized condensate to the boiler without additional pumps, valves, vents, or controls. There is zero water waste - all condensate returns to the boiler while still hot, saving energy, water, and boiler chemicals.